Growcase™
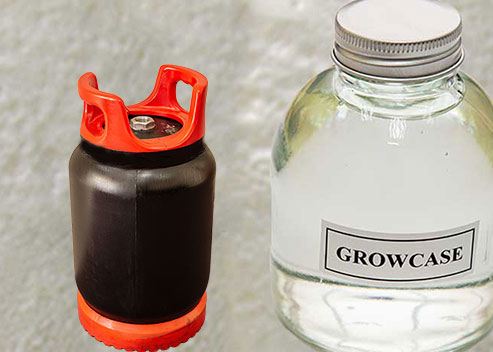
Product : Growcase™
Polyol blends for coating, adhesive, sealant and elastomer (CASE).
Application Information
Polyurethane Elastomers
Polyurethane elastomers have the characteristics of rubber, elastics. Sometimes, it also referred to thermoplastic polyurethane plastics (TPU). Polyurethane elastomers are used in a wide variety of end-use markets including footwear (shoe soles), automotive (dash board, skirting, steering wheel, body kits and arm rest), construction applications (window and door gasket, roofing membrane and water proofing) and machinery (belt, wheel and bearing).
Non-foaming elastomer. The materials produced by EL series has the hardness ranging from 20 to 80 shore D, high elasticity and tensile strength with elongation up to 200 % in size. Materials also have good compression, tear strength and resilience properties. Materials resist the absorption of water, attack by oils, solvents and oxygen, and deteriorate by UV. Materials are suitable to be used as coating, jacketing and protecting skin.

Reaction Injection Molding (RIM) is the result of a reaction between polyol blend and isocyanate as they are injected into a closed mould at low pressure. The two components are mixed together and fill up the mold cavity, then the chemical reaction takes place in the mold to produce structural plastic foams used for the automotive, medical and industrial industries. Depending on the formulation of polyol blend, RIM can be made in the hardness between 25 Shore A and 75 Shore D.
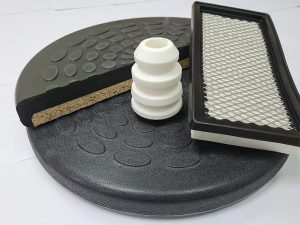
Integral skin foams or self-skinned foams are materials with a low-density foamed core surrounded by a nearly solid skin of the same material. This type of polyurethane foam moulding is ideal for many applications including grab handles, armrests, headrests and medical components with the hardness up to 90 shore A.
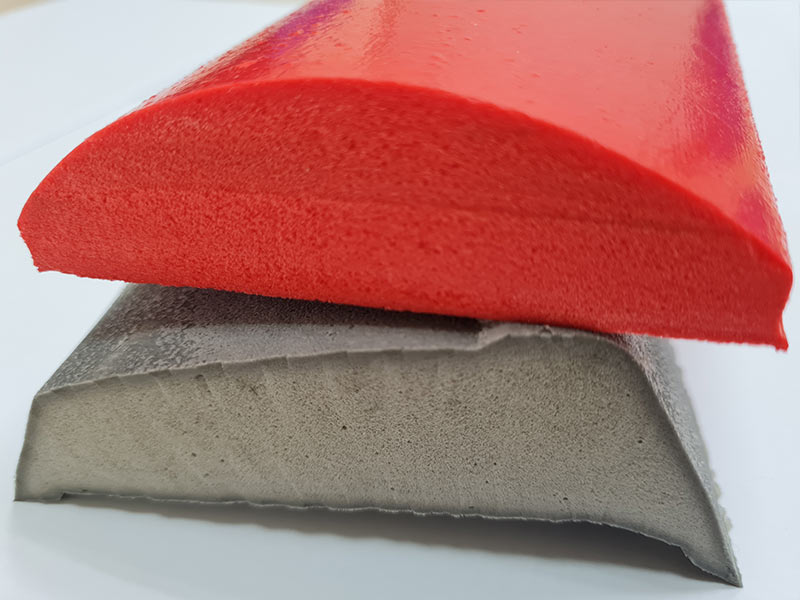